OK, I emailed RC engineering and what I now know is that the lowest value they have seen is 0.7 Ohms and the highest peak current required that they have seen is 9 Amps. Use those for your heat demands times 6 channels.
Fred.
Injector Control Options
Re: Injector Control Options
DIYEFI.org - where Open Source means Open Source, and Free means Freedom
FreeEMS.org - the open source engine management system
FreeEMS dev diary and its comments thread and my turbo truck!
n00bs, do NOT PM or email tech questions! Use the forum!
The ever growing list of FreeEMS success stories!
FreeEMS.org - the open source engine management system
FreeEMS dev diary and its comments thread and my turbo truck!
n00bs, do NOT PM or email tech questions! Use the forum!
The ever growing list of FreeEMS success stories!
Re: Injector Control Options
Interesting. Any word on the peak/hold ratios ?
Re: Injector Control Options
No, it took 2 emails to get that out of them :-)
If they haven't seen anything lower in impedance or higher in current demand, who would have?
I asked to get an idea of power output in heat.
On the bench one could use a potentiometer to adjust the current figures on the fly and observe when it failed to hold both statically (always on, just wind down the current until it closes) and dynamically, wind it down until flow/actual duty changes.
Fred.
If they haven't seen anything lower in impedance or higher in current demand, who would have?
I asked to get an idea of power output in heat.
On the bench one could use a potentiometer to adjust the current figures on the fly and observe when it failed to hold both statically (always on, just wind down the current until it closes) and dynamically, wind it down until flow/actual duty changes.
Fred.
DIYEFI.org - where Open Source means Open Source, and Free means Freedom
FreeEMS.org - the open source engine management system
FreeEMS dev diary and its comments thread and my turbo truck!
n00bs, do NOT PM or email tech questions! Use the forum!
The ever growing list of FreeEMS success stories!
FreeEMS.org - the open source engine management system
FreeEMS dev diary and its comments thread and my turbo truck!
n00bs, do NOT PM or email tech questions! Use the forum!
The ever growing list of FreeEMS success stories!
- Delta
- LQFP112 - Up with the play
- Posts: 111
- Joined: Fri Jul 25, 2008 8:04 pm
- Location: Perth, WA, Australia
Re: Injector Control Options
100hp/L is not the factor for deciding injectors - future power is - most people buy once. Not sure what its like the world over, but EVERY australian aftermarket EMS has drivers for low Z injectors. When people upgrade they tend to choose low Z unless they are flash tuning. Perhaps thats just the circles I am in (mostly turbo 6cyl and large v8)....but I doubt it - 100hp/L is actually pretty damn common now too. I'm making just under 130hp/L.Fred wrote:Yeah, only a fraction, how many cars that run standalones percentage wise do you think make more than 100hp per cylinder? That is easily supported by high Z injectors.Delta wrote:Only a fraction??
Key to who? You, Abe, and others, sure, but not to all potential users. Including it has its drawbacks. They can't be ignored, and if included they need to be handled very carefully. Even if we decide no low Z on board we aren't saying no low Z, we are just saying no low Z on board. Experience shows us that this does not deter many users. After all installing a second box with cylCount x2 +2 connections or so isn't exactly a big ask. Heaps of people use horrible resistor boxs with similar extra effort required.If you limit yourself to saturation onboard then you are basically not offering a solution that keeps up with 99% of aftermarket gear. While I understand this is an open source effort and hence does not HAVE to be up to the standard of a commercial product - removing a key feature to an external board or leaving it out entirely sounds very MSish.
Having said all that, I'm all for it IF we can do it in a NICE way overall. Perhaps put your circuit on there and just suggest a good case IF using low Z. That simplifies it and supports it. BUT, we need to check out the RF side of it in detail IRL before committing to that. Putting a massive noise source in the case like that MUST be done with great care.Later on we can start adding things like my injector driver, onboard IGBT ignition, boost control, closed loop idle etc etc. But I think the second revision definitely SHOULD contain all possible features inside one case - even if they are plug in boards internally.
Speaking of the car in your avatar, care to put up a thread about it in user rides? Looks coolBTW - If I'm testing anything it will be going on the car in my avatar - currently it runs an EMS8860 and I have low Z injectors - Siemens Deka 72lb/h to be exact, so I'll need peak and hold as they are 2.8ohms.
Also, looks like an old school 6 pot, did it have an ECU at all stock? I think not = one of the biggest reasons to go aftermarket. IE, old engine or blank slate setup.
Fred.
Key to MOST people who are comparing features. Like I said perhaps its the circles I'm in, or perhaps its an australian thing - but high hp and low Z injectors are VERY VERY common here. (and quite cheap too)
Yes noise is an issue - but every other aftermarket manufacturer is doing it so it can't be THAT hard. I've not noticed any noise problems with the EMS8860. I think you'll find with a good ground plane design and plenty of decoupling it won't be a problem.
hmm I probably won't post up about the car. Its not worth a whole thread. Its a 90's model falcon. 4L I6 OHC - The car came with an EEC-V and its still in there controlling the gearbox (for now - thats another little project). Now turbo, making ~520-550fwhp.
Re: Injector Control Options
I said per cylinder not per litre and I meant intended max, not current values.Delta wrote:100hp/L is not the factor for deciding injectors - future power is - most people buy once.
You should know that ozzy OWNS the world EMS market :-) Least, it seems that way to me.Not sure what its like the world over, but EVERY australian aftermarket EMS has drivers for low Z injectors.
Yeah, 100hp per litre is OEM naturally aspirated territory. My girlfriends corolla makes that much ;-)100hp/L is actually pretty damn common now too. I'm making just under 130hp/L.
That's common everywhere, but not everyone wants to make "high hp" where high is defined by me to mean > 200hp/L Those below that sort of figure don't need it, and those doing a budget build will be looking at OEM injectors and therefore high Z. I guess you have successfully illustrated the point here. The guy that buys the new garrett and HKS water pump and edelbrock manifold and perhaps siemens injectors is quite likely to buy a stinger EMS. I would say you are not representative of the typical DIY build. Most guys that aren't afraid to spend a bit on a build end up with a commercial EMS. Is your turbo an ebay hx52 or a off-shelf garrett/kkk/other-name-brand? I think we'd struggle to ever get all the $$/name guys to use this, AND I don't want them here either. The site is about dig in DIY people building their own stuff engine, car, and ecu. MS is riddled with a disease called "cheap arses looking to save cash by cutting corners". Typically they don't care about building it, hence the resellers sell built units, and plenty of them. The hard core DIY folk got left out in the cold and this is where we ended up :-) Don't take all that the wrong way, I'm just saying you are the exception, not the rule for the type of people likely to be using this in the short term :-)but high hp and low Z injectors are VERY VERY common here.
Sure, let's get on with it then. Those users that need it can use a good solid case with good dissipation, and those that don't can not care and will also be free of noise (if the design is flawed in that respect with regards layout).Yes noise is an issue - but every other aftermarket manufacturer is doing it so it can't be THAT hard. I've not noticed any noise problems with the EMS8860. I think you'll find with a good ground plane design and plenty of decoupling it won't be a problem.
Sure, but at least dedicate a thread to the engine bay! Looks cool, I'd like to see more detail, perhaps others would too.hmm I probably won't post up about the car. Its not worth a whole thread.
Fred.
DIYEFI.org - where Open Source means Open Source, and Free means Freedom
FreeEMS.org - the open source engine management system
FreeEMS dev diary and its comments thread and my turbo truck!
n00bs, do NOT PM or email tech questions! Use the forum!
The ever growing list of FreeEMS success stories!
FreeEMS.org - the open source engine management system
FreeEMS dev diary and its comments thread and my turbo truck!
n00bs, do NOT PM or email tech questions! Use the forum!
The ever growing list of FreeEMS success stories!
Re: Injector Control Options
Sorry I've been slacking on this.
A big part of what people are looking for is something that CAN do whatever they want. Native support for low-Z injectors is definitely something I would put in. It falls in the same category as supporting v-8's, or even 6 cyl to be honest. They are out there, there are many of them... What else do you want to know?
Oh, and... sorry about the dropping the 'hold' current, I was thinking about that pre-load thing, where you put some current through the injector in anticipation of opening it. Obviously hold current is essential.
It would be awesome if the drivers can be on board. Has anyone quantified the noise of these drivers? My guess is it isn't all that bad, most things I worry about turn out fine.
Throw caps at it.
-Abe.
A big part of what people are looking for is something that CAN do whatever they want. Native support for low-Z injectors is definitely something I would put in. It falls in the same category as supporting v-8's, or even 6 cyl to be honest. They are out there, there are many of them... What else do you want to know?

Oh, and... sorry about the dropping the 'hold' current, I was thinking about that pre-load thing, where you put some current through the injector in anticipation of opening it. Obviously hold current is essential.
It would be awesome if the drivers can be on board. Has anyone quantified the noise of these drivers? My guess is it isn't all that bad, most things I worry about turn out fine.

-Abe.
Re: Injector Control Options
Too strong of a flyback clamp (low voltage) will hurt the injector closing time and reduce precision of the injector control. A weak clamp will hurt the power dissipation of the system during PWM.
A strong clamp helps during the PWM period in two ways, with a low voltage drop across the clamp there's low power dissipated and also the current in the coil is sustained for longer after the driver turns off, requiring a smaller PWM duty cycle which means less power needed for the injectors (injectors stay cold and overloaded electrical system stays happy)
There was a design incorporated in Mega-you-know-what, originally available as an add-on board (not sure who designed that) but later incorporated on the main circuit board (v3.0) that used a dual driver, one switched to ground and the other switched to the +12V rail. The second driver prevents the voltage from going more than a couple volts above the +12V rail. The ground driver goes into PWM mode after opening the injector but the +12V driver stays on for the entire injector opening duration. Then when it's time for the injector to close, both drivers are switched off, letting the injector spike dozens of volts when it's closing.
This design incorporates a lot of components and two I/O channels for each injector but it works very well because it combines a high voltage clamp and a low voltage clamp. It's entirely possible to come up with a decent control with less parts and will require some experimentation as to where the sweet spot is for a compromise between closing time and current dissipation but this is the ideal situation (low V clamp during PWM, high V clamp when injector is closing).
One might also want to explore using a capacitor in parallel with the injector to reduce the amount of clamping required.
A strong clamp helps during the PWM period in two ways, with a low voltage drop across the clamp there's low power dissipated and also the current in the coil is sustained for longer after the driver turns off, requiring a smaller PWM duty cycle which means less power needed for the injectors (injectors stay cold and overloaded electrical system stays happy)
There was a design incorporated in Mega-you-know-what, originally available as an add-on board (not sure who designed that) but later incorporated on the main circuit board (v3.0) that used a dual driver, one switched to ground and the other switched to the +12V rail. The second driver prevents the voltage from going more than a couple volts above the +12V rail. The ground driver goes into PWM mode after opening the injector but the +12V driver stays on for the entire injector opening duration. Then when it's time for the injector to close, both drivers are switched off, letting the injector spike dozens of volts when it's closing.
This design incorporates a lot of components and two I/O channels for each injector but it works very well because it combines a high voltage clamp and a low voltage clamp. It's entirely possible to come up with a decent control with less parts and will require some experimentation as to where the sweet spot is for a compromise between closing time and current dissipation but this is the ideal situation (low V clamp during PWM, high V clamp when injector is closing).
One might also want to explore using a capacitor in parallel with the injector to reduce the amount of clamping required.
Re: Injector Control Options
I thought it mattered more than you other guys make out.
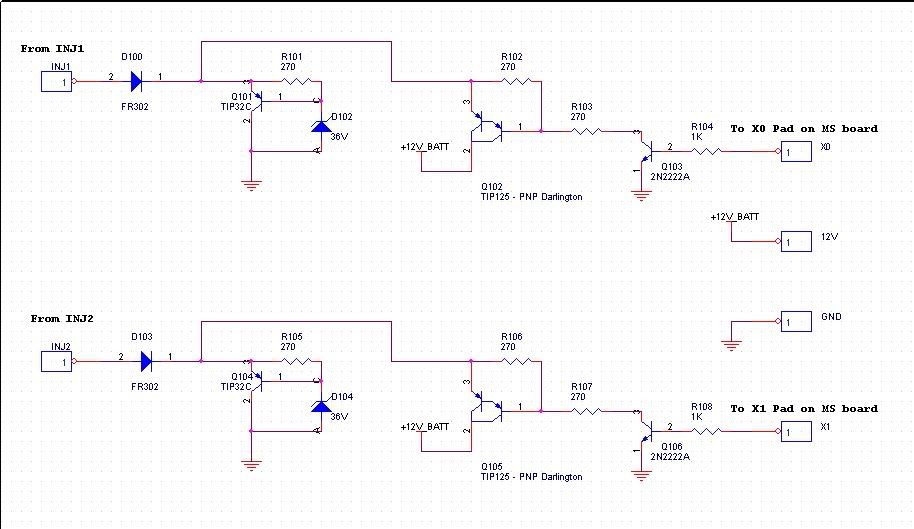
Thanks for posting Baldur, it's been a long time since you said much on any site like this :-)
Fred.
Note, the low clamp would be to 12v with a straight diode or transistor setup whereas the high clamp could be to ground OR 12v.baldur wrote:A strong clamp helps during the PWM period in two ways, with a low voltage drop across the clamp there's low power dissipated and also the current in the coil is sustained for longer after the driver turns off, requiring a smaller PWM duty cycle which means less power needed for the injectors (injectors stay cold and overloaded electrical system stays happy)
Here it is :There was a design incorporated in Mega-you-know-what, originally available as an add-on board (not sure who designed that) but later incorporated on the main circuit board (v3.0)
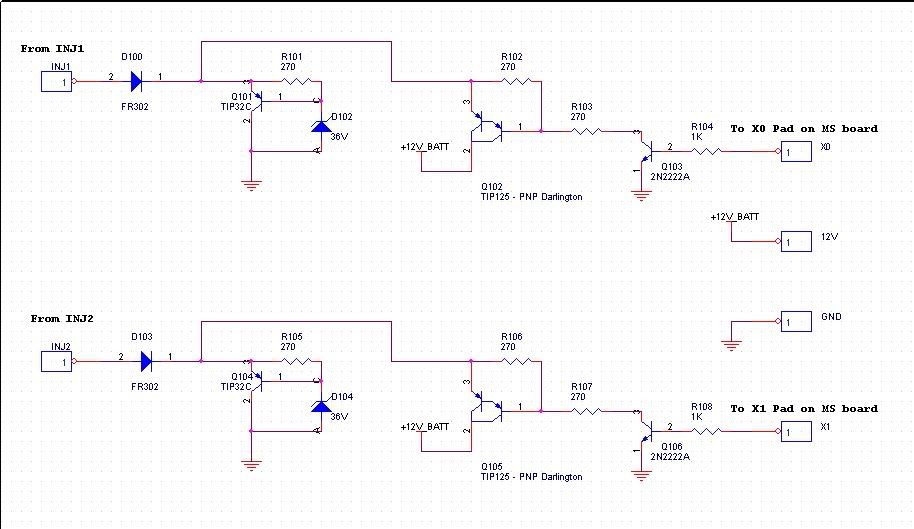
I fail to see why a single CPU channel isn't enough. Low clamp from switch on to switch off and high clamp always.This design incorporates a lot of components and two I/O channels for each injector but it works very well because it combines a high voltage clamp and a low voltage clamp. It's entirely possible to come up with a decent control with less parts and will require some experimentation as to where the sweet spot is for a compromise between closing time and current dissipation but this is the ideal situation (low V clamp during PWM, high V clamp when injector is closing).
Delta, doesn't your setup incorporate a cap in a similar fashion to this?One might also want to explore using a capacitor in parallel with the injector to reduce the amount of clamping required.
Thanks for posting Baldur, it's been a long time since you said much on any site like this :-)
Fred.
DIYEFI.org - where Open Source means Open Source, and Free means Freedom
FreeEMS.org - the open source engine management system
FreeEMS dev diary and its comments thread and my turbo truck!
n00bs, do NOT PM or email tech questions! Use the forum!
The ever growing list of FreeEMS success stories!
FreeEMS.org - the open source engine management system
FreeEMS dev diary and its comments thread and my turbo truck!
n00bs, do NOT PM or email tech questions! Use the forum!
The ever growing list of FreeEMS success stories!
- Delta
- LQFP112 - Up with the play
- Posts: 111
- Joined: Fri Jul 25, 2008 8:04 pm
- Location: Perth, WA, Australia
Re: Injector Control Options
My design does all of this and only requires one output pin - did you read through the whole thread???baldur wrote:Too strong of a flyback clamp (low voltage) will hurt the injector closing time and reduce precision of the injector control. A weak clamp will hurt the power dissipation of the system during PWM.
A strong clamp helps during the PWM period in two ways, with a low voltage drop across the clamp there's low power dissipated and also the current in the coil is sustained for longer after the driver turns off, requiring a smaller PWM duty cycle which means less power needed for the injectors (injectors stay cold and overloaded electrical system stays happy)
There was a design incorporated in Mega-you-know-what, originally available as an add-on board (not sure who designed that) but later incorporated on the main circuit board (v3.0) that used a dual driver, one switched to ground and the other switched to the +12V rail. The second driver prevents the voltage from going more than a couple volts above the +12V rail. The ground driver goes into PWM mode after opening the injector but the +12V driver stays on for the entire injector opening duration. Then when it's time for the injector to close, both drivers are switched off, letting the injector spike dozens of volts when it's closing.
This design incorporates a lot of components and two I/O channels for each injector but it works very well because it combines a high voltage clamp and a low voltage clamp. It's entirely possible to come up with a decent control with less parts and will require some experimentation as to where the sweet spot is for a compromise between closing time and current dissipation but this is the ideal situation (low V clamp during PWM, high V clamp when injector is closing).
One might also want to explore using a capacitor in parallel with the injector to reduce the amount of clamping required.
Re: Injector Control Options
Delta, I've read through your massive monolithic paragraph about your circuit a few times in a row now and I don't understand the snubbing fully or it doesn't behave as Baldur suggested it should.
I understand the pwm and current limit features etc, but I don't get the fly back catching mechanism fully.
Can you explain again how that works for some simple minded noobs like me and me to understand please?
Fred.
I understand the pwm and current limit features etc, but I don't get the fly back catching mechanism fully.
Can you explain again how that works for some simple minded noobs like me and me to understand please?
Fred.
DIYEFI.org - where Open Source means Open Source, and Free means Freedom
FreeEMS.org - the open source engine management system
FreeEMS dev diary and its comments thread and my turbo truck!
n00bs, do NOT PM or email tech questions! Use the forum!
The ever growing list of FreeEMS success stories!
FreeEMS.org - the open source engine management system
FreeEMS dev diary and its comments thread and my turbo truck!
n00bs, do NOT PM or email tech questions! Use the forum!
The ever growing list of FreeEMS success stories!